Upon returning from being on the West Coast for July, Alice & I hustled a bit to get a new rocket of hers ready for the August PARA launch just a few days later:
It’s a Stretch Stubby kit from ASP that we received as a surprise gift in an order from a Fourth-of-July sale. It’s one member of a family of “Stubby” rockets from ASP, the other, shorter, ones being actually stubby. We were immediately intrigued to see that the rocket’s made up of several sections of tube, not one. That meant we could convert the kit just a bit so that it can be prepped and launched with any combination and ordering of the sections. Seeing how easy it’d be, I was actually a bit surprised the kit wasn’t designed explicitly to do so. In any event, having distinct sections like that would make it really easy for Alice to paint them in different colors. She was also very interested in being able to change the configuration before each flight. So she got to work on a sketch of her desired paint scheme and I made up a simulation model to evaluate the stability of different length configurations.
Design & Construction
It turned out all of the configurations were projected to be stable without modification except for flying with solely the tail and nosecone. To add just a little challenge, shifting the center of gravity far enough ahead of the center of pressure in that minimal setup would require a lot of weight if added at the base of the nosecone—the weight would be practically right at the center of pressure given the minimal body length. The ballast had to go at the very tip of the nosecone, and ideally only in this configuration. So I swapped the gorgeous BT-60 MS balsa nosecone from the kit with a plastic one I had laying around. I cut the shoulder open and made a 3D printed screw-in compartment that could be epoxied into the tip. With more time I would have designed & printed a whole nosecone with an integral compartment, but we were on a tight schedule. That compartment provides a place to firmly secure varying weights right at the farthest forward point of the rocket. It also holds the weight in a fixed position rather than swinging about if it was just clipped to the line. The hollow nosecone also let the parachute be packed inside, shifting that weight forward as well. The compartment’s plug additionally serves as the tie down anchor for the shock cord. After unscrewing it and unhooking the parachute’s snap swivel attachment, the line passes easily through the tube sections for swapping them in and out.
After assembling the rocket together, Alice painted it precisely to her previously devised specifications. Her spray painting has improved quite visibly the past few months. Size and weight of the cans is still a challenge, even with a pistol grip attachment, but she’s gotten vastly better at not spraying the paint on too thickly in one go. This time she did though thoroughly entertain herself by “accidentally” heavily spray painting my hand purple while I was holding the nosecone for her. Periodically for days afterward she would randomly stop amid some other activity and ask “Daddy, why’s your hand purple??” and cackle wildly.
In the end, having constructed, finished, and weighed everything to update the simulation with real numbers, a 20g fishing weight tucked into the compartment was projected to make the minimal configuration satisfactorily stable.
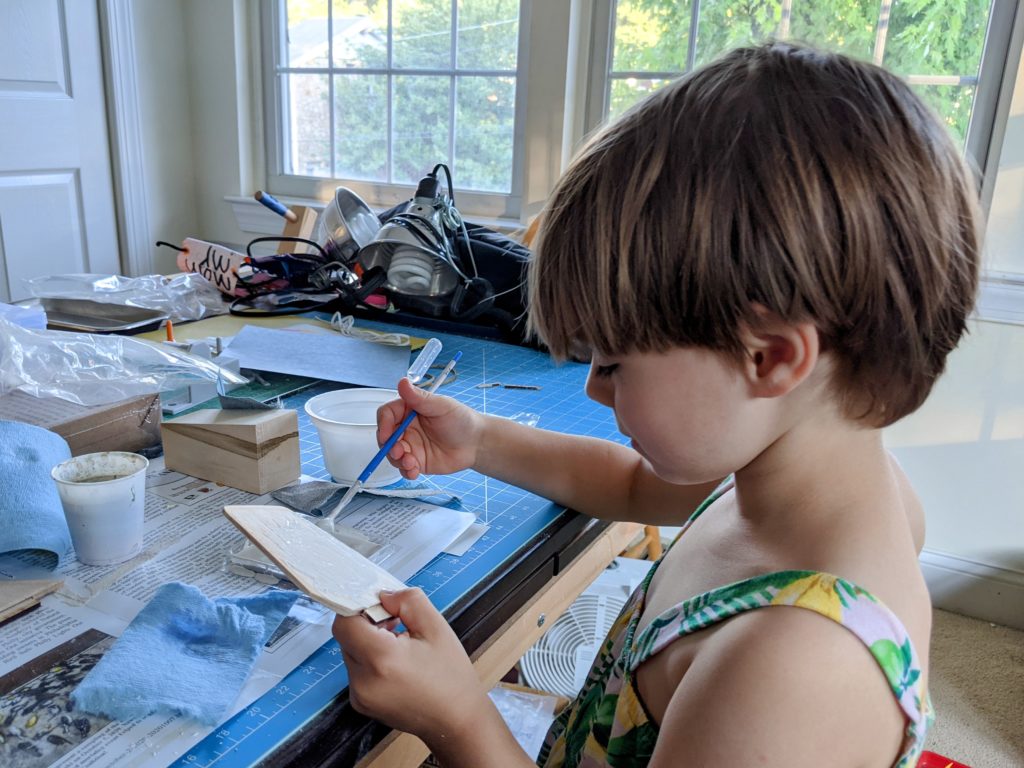
Covering a fin with sandable wood sealer so they can be smoothed out (full disclosure, this is a fin for another rocket we did a little work on at the same time but haven’t finished yet).
First Launch
Our first launch of the completed-just-in-time rocket was pretty successful. However, after that one just-slightly-creepy retrieval from deep in the corn, and rightly afraid of losing the rocket forever amid the field of 7+ foot tall stalks, Alice decided to call the day a success without trying out all configurations of the rocket. She says we’ll do that once the harvest is done…